자동차 부품 산업에 3D 프린터 도입 가속화
- 기자명 전인호 기자
- 입력 2018.11.16 10:18
- 댓글 0
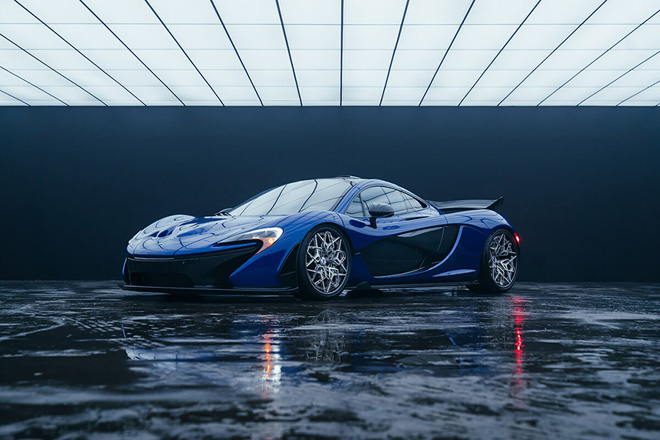
3D 프린터로 제작한 자동차 부품 도입이 가속화되고 있다. 독일의 자동차 제조사 BMW와 애프터마켓 휠 제조사 HRE 퍼포먼스 휠은 진보된 3D 프린터 기술을 실제 부품 생산에 적극적으로 도입할 계획이다.
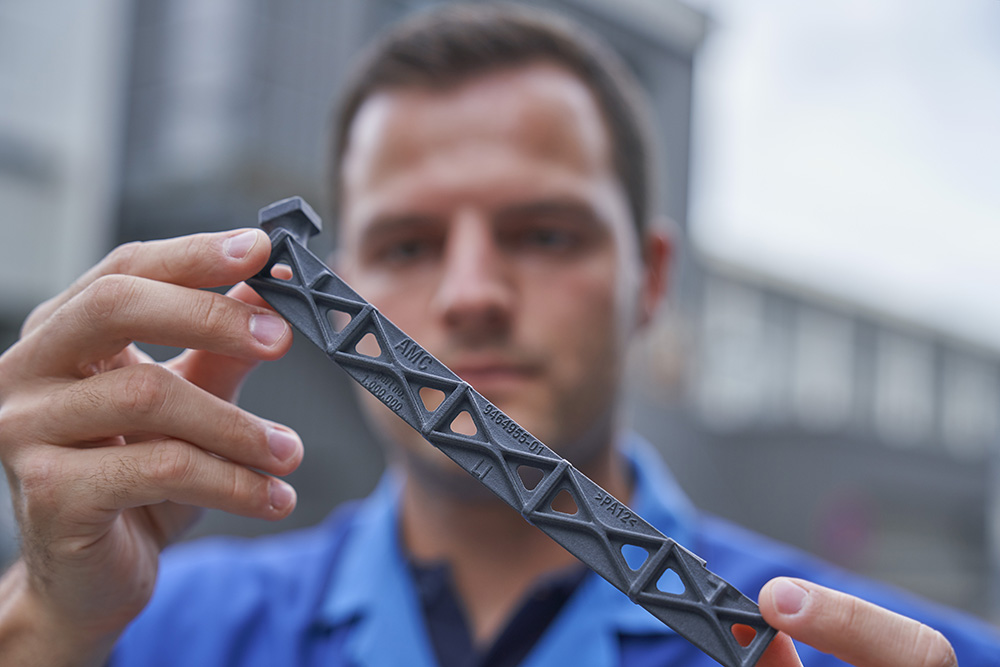
BMW는 고객 맞춤형 부품 제조 공정에 대대적으로 3D 프린터를 활용한다. 소량 생산의 맞춤형 부품 또는 형상이 매우 복잡한 부품이 해당된다. 이전까지는 3D 프린터로 제작한 부품이 프로토타입 모델 개발에 활용됐다.
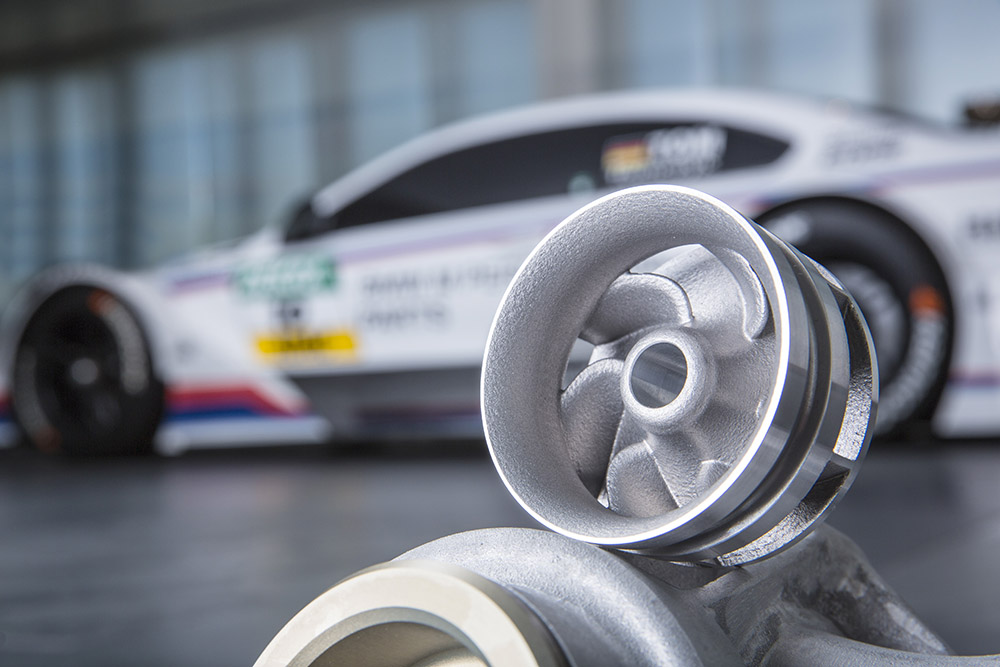
또한 BMW 그룹은 2010년 최초로 3D 프린트로 제작한 워터펌프 임펠러를 DTM 레이싱 머신에 사용한 바 있다. 또한 i8 로드스터 모델의 소프트톱 커버의 알루미늄 브라켓은 3D 프린터로 제작한 부품이기도 하다. 공장 내 근로자들이 사용하는 각종 장비도 3D 프린터로 만들어 사용 중이다.
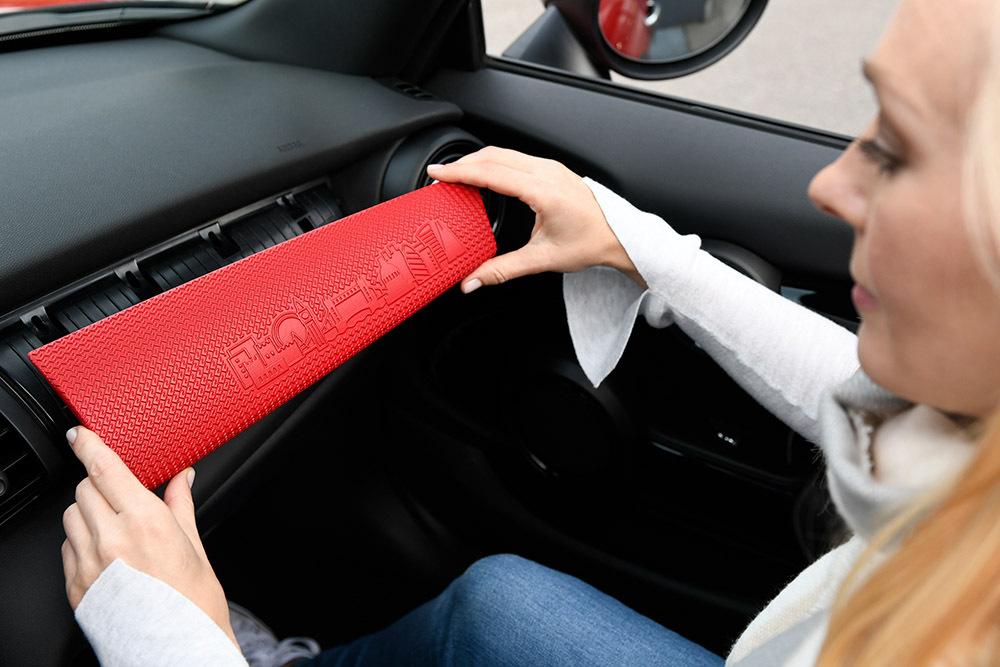
미니 브랜드의 소비자 맞춤형 패키지의 부품도 3D 프린터로 제작한다. 또한 독일 뮌헨에 위치한 연구 개발 센터에는 연간 약 14만 개의 프로토 타입 부품을 3D 프린터로 제작하여, 다양한 분야에 공급하고 있다.
HRE 퍼포먼스 휠은 자사 첫 번째로 3D 프린터 제작한 경량 티타늄 휠을 소개했다. HRE3D+라는 모델명의 이 휠은 HRE와 제너럴 일렉트릭(General Electric’s)의 자회사 아캄(Arcam)과 파트너십을 통해 개발됐다.
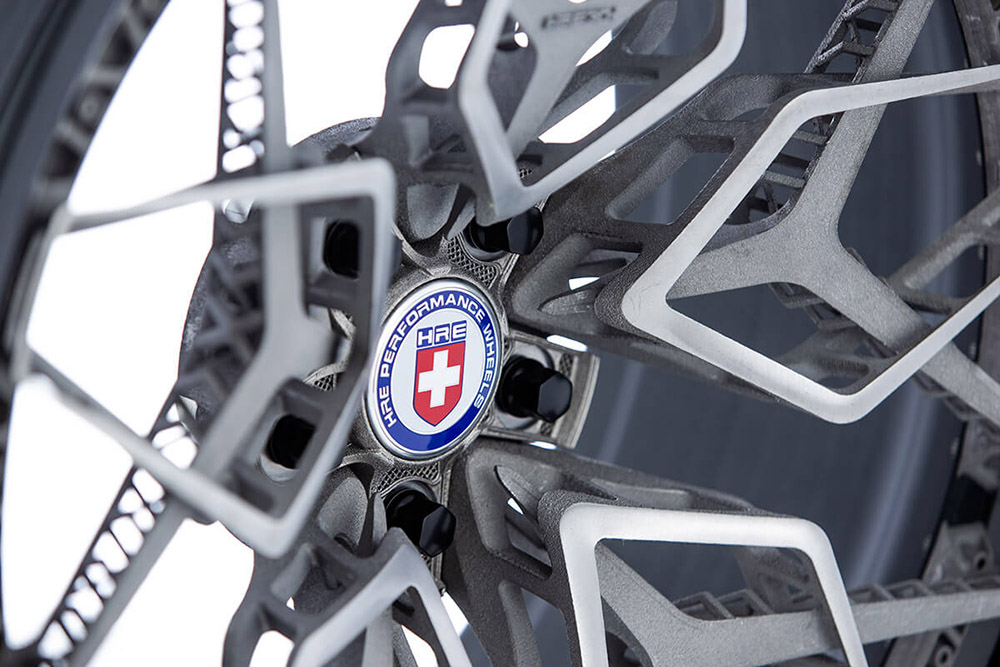
HRE는 CAD를 사용하여 HRE3D+를 설계했다. 한편 아캄은 자사의 전자빔 용해(Electron Beam Melting) 머신을 활용, 티타늄 분말로 복잡한 디자인의 휠 림을 제작해냈다. 3D 프린터를 사용한 공정은 기존의 단조 방식보다 효율적이라는 것이 이들이 3D 프린터 공정을 긍정적으로 바라보는 이유다.
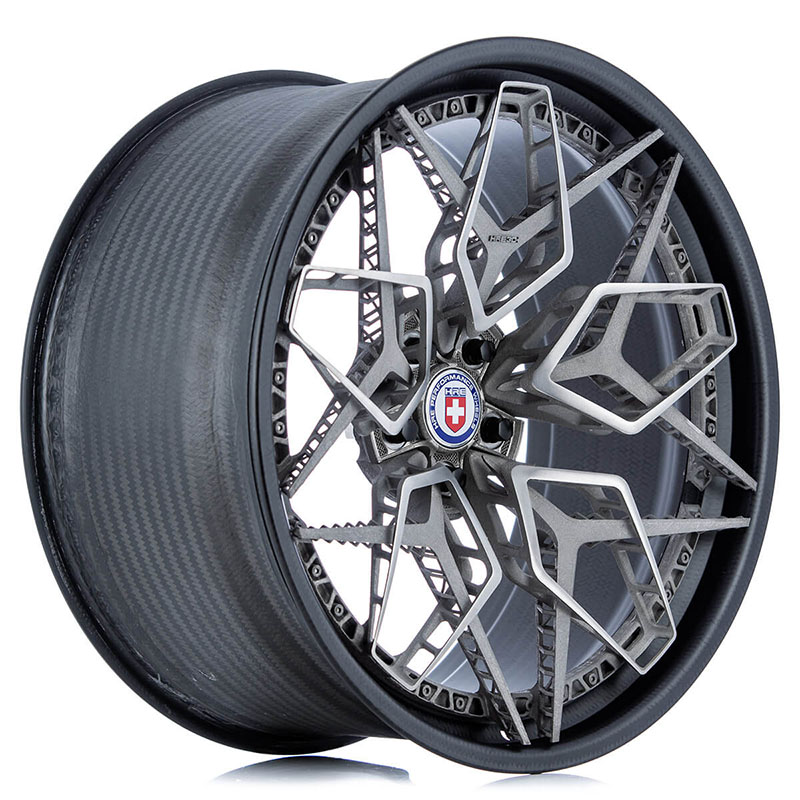
HRE에 따르면 기존의 단조 방식으로 모노 블록 휠을 제작할 경우 알루미늄 100파운드(45.35kg) 중 80%를 깎아내야 하는데 반해 3D 프린터 공정은 5%만의 소재가 제거되기 때문에 재활용 측면에서도 보다 효율적이라고 언급했다.
한편, BMW 그룹은 지금까지 3D 프린터로 100만 개의 부품을 생산했다. 3D 프린터를 이용한 2018년 BMW 그룹의 부품 생산은 전년 대비 42% 증가한 20만 개를 달성할 것으로 기대된다.